Quality Assurance in Construction
High-quality and legally-compliant buildings should be the main aim of all construction firms. Ensuring the client’s expectations are met, buildings are consistently safe and high standards are maintained throughout, are what enhance a company’s reputation and ensure construction projects finish on-budget and on-time. In this article, we’ll look at what quality assurance in construction is, why it’s important, the key components of a quality assurance plan, and provide a few tips on how to implement quality assurance in construction projects.
What is Quality Assurance in Construction?
Quality assurance (QA), which is also sometimes referred to as Construction Quality Assurance (CQA), is a way of being prepared, making the best decisions, ensuring a high-quality finish and avoiding errors throughout the lifecycle of a project.
In construction, quality assurance is essential. Selecting the right materials from the right suppliers, using the correct tools and people for the job, ensuring everyone is working to the same standards and timeframes, and preventing costly building mistakes, are all vital for the success of a project.
To ensure success, quality assurance in construction means having policies, procedures and standards in place that guide the construction project from start to finish, ensuring high quality and high efficiency at all stages of the project, so that both the client’s and the industry’s expectations are met.

What is the Difference Between Quality Control and Quality Assurance?
Quality assurance (QA) and quality control (QC) are two separate things but both are generally used together throughout every construction project. Whilst QA is more proactive, QC is often more reactive.
Quality assurance (QA) is about setting standards and preventing problems before they occur. As the name suggests, QA gives everyone the assurance that high quality will be achieved throughout the construction project, whether it’s related to the materials and suppliers used, skills of the workers that are hired or legal compliance of the project. The standards set by QA must be maintained throughout the construction process and act as the basis for all decisions made.
Quality control (QC) is about checking whether the elements of the construction project meet the expected standards through regular audits, inspections and quality checks. If the expected standards aren’t being met, then corrective action is needed to get the project back on track. QC ensures that faults and problems are resolved and that the end product meets the expectations of both clients and industry regulators.
Importance of Quality Assurance in Construction
The importance of quality assurance in construction cannot be underestimated. When implemented well, QA not only ensures a high-quality finish, it also:
- Ensures the project runs on time, on budget and without setbacks.
- Ensures each construction project meets industry health and safety standards.
- Reduces the chances of penalties due to legal non-compliance.
- Ensures buildings are well-planned to be durable, sustainable and practical.
- Reduces the likelihood of costly mistakes occurring.
- Helps to identify issues before they arise.
- Mitigates costly rebuilds or reworks due to standards not being met.
- Enhances the construction company’s reputation.
- Guarantees client satisfaction as their specifications are met.
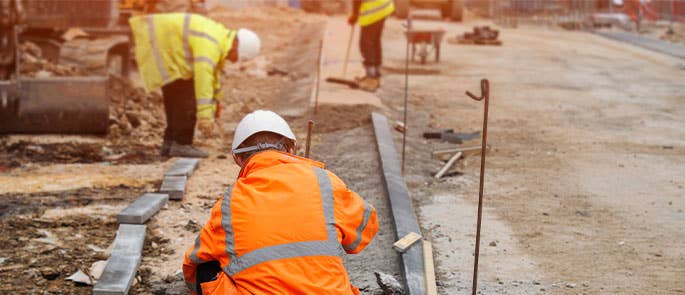
Construction Quality Assurance Plan
A construction quality assurance plan (CQA Plan) is a written management system that can be used for any type of construction project. The information contained in a construction quality assurance plan should be tailored to the specific site or project, but generally includes aspects such as:
- What the quality standards are.
- QA procedures for each step of the project.
- Decision-making procedures for each stage of the project.
- Proposed corrective action if issues are identified.
- Minimum acceptance criteria.
- Who has responsibility for QA.
- Detailed design descriptions.
- Scale drawings, maps and plans.
- Material specifications.
- Names of suppliers and subcontractors.
- Procedures for qualifying suppliers and subcontractors.
- Installation procedures.
- Conformance testing information.
- Details of any other assessments or testing required.
- Details on project completion inspections.
Quality assurance plans are a key part of an effective quality management system (QMS). A QMS can be used by your organisation to help ensure client specifications are met and that your construction project delivers what it promises. Its aims are to help you to continually improve your processes, enhance the quality of your products and continually exceed customer expectations. Find out more about implementing a certified QMS in our article: ISO 9001 – Quality Management System.
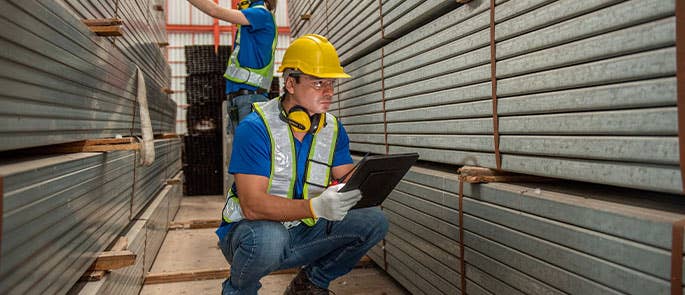
How to Implement Quality Assurance in Construction
When looking to implement quality assurance in construction, there are a number of useful steps you may wish to follow to ensure your QA system is as effective as possible:
Hire the right people – to ensure quality standards are met, it’s important to use the right people for the job. Check people’s skills and certificates, use competent contractors and subcontractors and find designers, architects, suppliers and project managers with proven experience of your site and its materials. Furthermore, everyone on-site must have a unified understanding of what quality means and what the expectations are.
Cross-check your suppliers – all the tools, materials and equipment used in your construction projects must be of the highest quality to ensure the end result meets expectations. Avoid cutting corners by buying low-cost, low-quality materials, as this will only cost you more in the long run. Similarly, be sure to verify your suppliers to make sure they can meet your demands and standards and, if they can’t, compare them with other suppliers and find a better fit.
Start QA early – the quality assurance process must start before the construction project begins and is an important part of the project planning stage. Ensure all checks, assessments and certifications are done and obtained well ahead of time so any potential problems or hold-ups can be resolved early, preventing costly project delays.
Monitor constantly – for QA to be effective, you need to be constantly checking the project against your standards and conducting regular quality checks. This responsibility can be shared out amongst site managers, as long as everyone is working to the same expectations and is confident to document and communicate any issues found. QA checks can be done via daily inspections but should be carried out at all stages of the project, from the first day on-site to the final snagging and handover stages.
Train everyone – everyone involved in the construction project needs to understand the importance of quality assurance in construction. This means training everyone in what quality means, how to ensure it and what to do if an issue arises. This can be done through initial staff training as well as regular toolbox talks. Everyone should be held to the same standards, no matter their role.
Seek to improve the QA process – after completion of every project, collect feedback from all of the stakeholders to assess your QA process and learn what worked well and what needs improvement for next time. These project reviews are an important part of the QA process as they help to ensure future QA processes operate effectively.
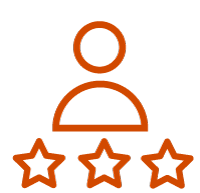
Want to Learn More?
Our range of online Health and Safety Courses helps construction site managers and employers train their staff quickly and correctly, ensuring quality standards and regulatory requirements continue to be met.
Quality assurance in construction is vital for ensuring construction projects are completed to schedule, on-budget and according to both client and regulatory standards. A thorough QA process means that all aspects of the project are carefully considered, resulting in a high-quality build that exceeds client expectations and enhances the reputation of your construction firm.
Further Resources:
- Health and Safety Courses
- What is ISO 9001 – Quality Management System?
- How to Build Relationships in Construction
- What is the Building Safety Act (BSA)?