Grinding Safety Precautions and Control Measures
There are many hazards involved in working with abrasive wheels for grinding. These range from immediate physical hazards, such as abrasions from wheel contact or dangerous projectiles from wheel breakage, to life-threatening health hazards, including hand-arm vibration syndrome (HAVS) from vibrations and pulmonary diseases from grinding dust.
With so many potential risks to workers, it is essential that you put safety precautions in place to eliminate or manage them to reduce the risk of grinding related incidents and accidents. In fact, as an employer, you have a legal duty to identify and apply appropriate control measures in your workplace to reduce the risks to health and safety created by grinding.
In this article, we will explain what grinding safety precautions are and how they can be identified and implemented using a grinding risk assessment and provide you with grinding safety tips to keep your workers safe and healthy. This article also includes a free, downloadable risk assessment template that you can use to identify grinding hazards and control measures in your specific workplace.
What are Grinding Safety Precautions?
Working with any kind of moving machinery is hazardous and can cause damage to property, injuries, illness and even death when operated incorrectly or without appropriate safety precautions in place.
Safety precautions, also known as control measures,can be implemented to reduce the risk posed by a certain hazard, mainly by reducing human exposure to that hazard.
The aim of a control measure is to eliminate a hazard completely but this isn’t always possible. For example, an abrasive wheel can break despite numerous safety precautions being taken. However, implementing these measures will greatly reduce the likelihood of a wheel breaking, and therefore, the risk for those involved.
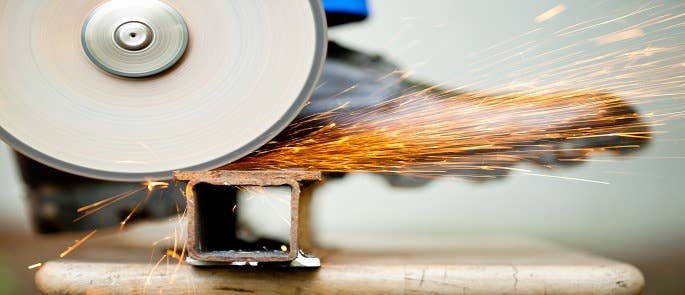
When implementing control measures to minimise workers’ exposure to grinding hazards, there is a priority order in which you need to apply these controls. This is called the hierarchy of control and the order is based on which control will most effectively prevent workers from being exposed to a hazard, thereby keeping them as safe as possible.
You should aim to achieve the highest level of control on the hierarchy of control but if you cannot achieve this, then you should aim for the next level of control until you can implement one suitable. While the first two steps on the hierarchy aim to eliminate a hazard altogether, the final three are about reducing the risk a hazard poses.
The hierarchy of control is:
- Elimination – removing the hazard altogether.
- Substitution – substituting the hazard for something else – for example, using a less dangerous machine instead of a grinding machine. This can be difficult if you are performing a specialised task that only one type of machine can perform.
- Engineering controls – this may involve isolating, enclosing or guarding the hazard to keep workers safe.
- Administrative controls – this involves changing the way people work to restrict their access to a hazard or how they interact with it and should involve employee training.
- Personal protective equipment (PPE) – this is when workers are provided with specific equipment to protect them against hazards and is the least effective control method for preventing harm.
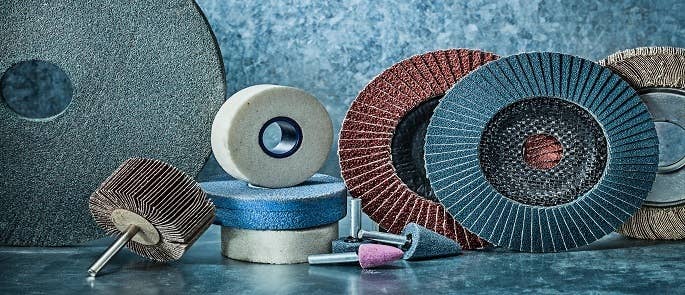
The use of abrasive wheels is regulated by the Provision and Use of Work Equipment Regulations act 1998 (PUWER) which legislates how machinery should be handled and operated to keep workers as healthy and safe as possible.
As an employer, you are legally required to conform with these regulations if abrasive wheels are used in your workplace.
Under PUWER, you must ensure that all machinery used in your workplace, including grinding machinery, is:
- Suitable for its intended purpose.
- Safe for use.
- Properly maintained and regularly inspected by a competent and trained individual.
- Operated, supervised and managed by competent and trained individuals, only.
- Accompanied by suitable health and safety measures and controls.
We will go into more detail about some of the health and safety measures you can put in place to control grinding hazards in your workplace later in this article. However, you first need to identify the specific hazards relevant to your workplace that need to be controlled.This can be achieved through carrying out a risk assessment.
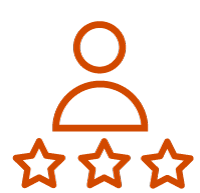
Looking to Learn More?
If your job role involves grinding and the use of abrasive wheels, our Abrasive Wheels Training course teaches you about the risks of using abrasive wheels and how to work safely with them, according to legal requirements, by putting the appropriate control measures in place.
Grinding Risk Assessment
PUWER requires employers whose employees use grinding machinery to carry out a risk assessment of the machinery and processes involved.
An abrasive wheel risk assessment should identify any potential and existing hazards associated with grinding in your workplace and the control measures that should be put in place to eliminate or reduce the risk they pose to workers.
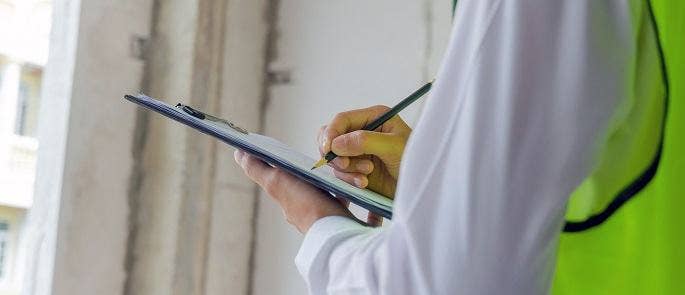
There are five key steps to performing a grinding risk assessment, including:
- Identifying hazards
Make a list of any hazards that could arise from grinding in your workplace. You can take a look at our article on the hazards of grinding for a list of common workplace grinding hazards, here. Just remember that this list is not exhaustive, your workplace may have different hazards that also need to be controlled and the risk assessment should be tailored to your specific needs
- Determine who may be harmed by each hazard
You next need to decide who is most likely to be harmed by each of the identified hazards and how this could happen. For grinding, this is most likely to be the person operating the machine, but other workers in that environment could also be harmed – for example, by dust in the air, sparks or projectiles.
- Evaluate the level of risk and decide control measures
You then need to determine the level of risk – low, medium or high – that each hazard poses. Use this ranking to decide which control measures are appropriate to eliminate or reduce exposure to that hazard.
- Record findings and implement control measures
If your workplace employs five or more people, then legally you must record the findings of your risk assessment. It is also essential that you implement the control measures you have identified in your workplace as soon as possible, including training staff on these changes.
- Regularly review your risk assessment
Your risk assessment should be reviewed regularly to identify any new grinding hazards or hazards that are not being effectively managed by the existing control measures. If these are identified, the risk assessment must be updated and new controls decided. This is necessary, for example, if new grinding machinery or processes are introduced or you have new staff.
Below we have provided a free risk assessment template that you can download and adapt for use in your workplace to help you identify and control the hazards of grinding.
Grinding Safety Tips
Control measures must be put in place to manage the risks posed by grinding to the health and safety of workers. The following list outlines some health and safety control measures that can be put in place in your workplace to reduce workers’ exposure to grinding hazards and keep them safe at work.
Employee Training
Under PUWER, employers must ensure that anyone they employ to use, repair, modify or perform maintenance or servicing on abrasive wheels is sufficiently trained to do so. This will ensure that workers understand the risks involved in using abrasive wheels and can implement the appropriate health and safety precautions at all times.
As an employer, you are responsible for ensuring your workers have this level of training, which should cover, at a minimum:
- Any hazards and risks that can arise from using abrasive wheels and the precautions that can be taken to control these.
- The marking system for abrasive wheels. If you’d like to learn what the markings on abrasive wheels mean, consider reading our article, here.
- How to transport and store abrasive wheels.
- How to inspect and test abrasive wheels for damage.
- The functions of each component used with abrasive wheels, such as flanges or blotters.
- How to assemble an abrasive wheel correctly to ensure they are balanced correctly
- How to dress an abrasive wheel.
- How to correctly adjust the work rest on a grinding machine.
- Use of appropriate grinding safety PPE.
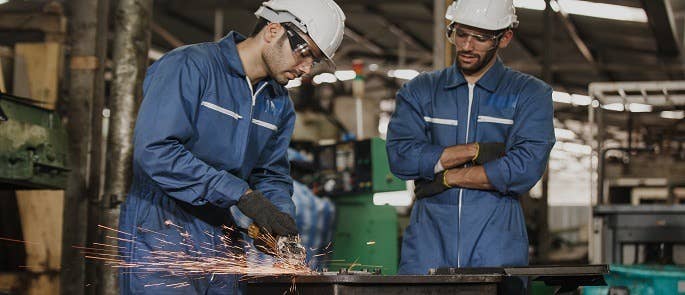
Appropriate Equipment
Using inappropriate equipment for grinding is a hazard. Machine operators must ensure that the abrasive wheel they use is fit for purpose, meaning it is compatible with both the grinding machine being used and the task being performed. Different wheels perform different functions depending on their properties, and using the wrong wheel can lead to fractures and breakage.
If you want to know more about the different classifications of grinding wheels, take a look at our article, here.
You should also make sure that any grinding machinery in your workplace has the following safety features:
- Suitable operating controls that are easy to see and use and which don’t allow the machine from being switched on by mistake.
- An emergency stop function that is easy to locate and use.
- A failsafe function for if the machine malfunctions.
Storing, Handling and Installation
The way your abrasive wheels are stored, handled and installed prior to use in grinding machines can make them more or less hazardous when operated.
Some measures for reducing this risk include:
- Ensuring anyone who installs grinding machinery in your workplace is qualified to do so, meaning they can recognise signs of damage to the wheel and know when a wheel is unfit for purpose.
- Storing grinding tools as close to the grinding location as possible, in a dry location protected from excessive vibrations. This reduces the risk of damage and eventual breakage.
- Handling wheels carefully to avoid dropping or bumping them and avoiding rolling wheels wherever possible.
- Transporting wheels using conveyors with adequate support, particularly for large wheels.
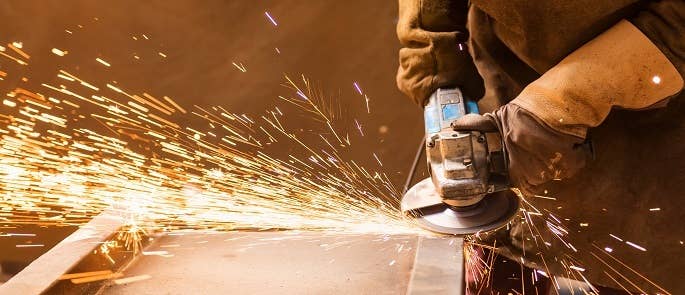
Safe Systems of Work
One of the main causes of harm while grinding is improper operation of machinery. This is why employee training is so important.
To reduce the risk to health and safety when operating grinding machines, operators should:
- Check the wheel is balanced before applying the workpiece. An out of balance wheel will emit strong vibrations, increasing the risk of HAVS and the wheel breaking. Redressing a wheel can improve its balance in most cases and wheels should be lightly dressed on a regular basis.
- Never apply excessive force to the wheel with the workpiece. This could cause the operator to slip and make contact with the wheel or cause the wheel to develop stresses and flat spots, making it vulnerable to breakage.
- Apply gradual, even pressure to the wheel with the workpiece, rather than hitting it with force.
- Only grind on the outer surface of the wheel. Never grind on the side of the wheel unless advised to do so by the manufacturer. This can lead to wheels bursting or workpieces becoming stuck between the wheel and work rest.
- Ensure the work rest is always adjusted as close as practicable to the wheel and kept secure.
- Make sure that the speed of the wheel does not exceed what is marked on the wheel by the manufacturer. Overspeeding causes wheel breakage.
- Never use a grinding machine, or any moving machinery, under the influence of illegal drugs, alcohol or some prescription drugs.
- Take regular breaks from grinding and exercise their hands during breaks to reduce the risk of HAVS.
The Working Environment
There are some changes that can be made to the environment where grinding work is being carried out to reduce exposure to hazards for the operator and other workers.
These include:
- Ensuring the environment is spacious enough that the machine operator is not at risk of being bumped while working, particularly if they work with portable grinders.
- Making sure the environment is well ventilated so that grinding dust is removed from the air, protecting workers from health issues.
- Making sure the space where grinding is taking place is uncluttered, particularly from anything flammable as abrasive wheels produce sparks that could easily cause a fire or explosion.
- Using a machine guard to reduce the risk posed by offsets from grinding, such as sparks, abrasive particles and projectiles and reduce the risk of the operator making contact with the machine. Make sure the material used for the guard is strong enough to withstand the potential forces on it.
Where practicable, grinding machines should be restricted to the person using them to reduce unnecessary risk to other workers. This is the best way to protect them from health hazards like noise and dust.
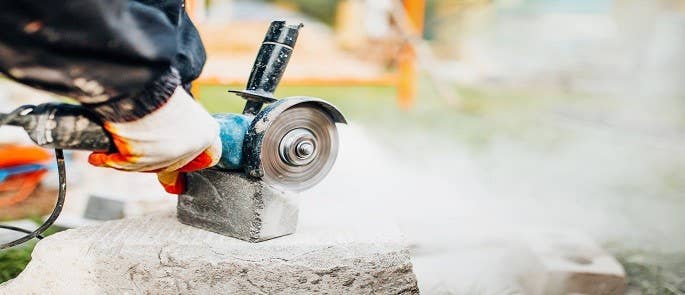
Inspection, Testing and Maintenance
Often, a visual inspection of an abrasive wheel before use can help to identify hazards. To manage these hazards, you should:
- Visually inspect the wheel before every use to make sure it has not become damaged through handling, storage or use. Damaged wheels are more fragile and prone to breaking.
- Ensure wheels are inspected and tested regularly by a trained person to identify any maintenance or cleaning needs.
- Label wheels with the date you received them, making sure to use older wheels before newer ones.
- Ensure new or refitted wheels are tested by the operator for one minute before being used. This gets the wheel up to speed and allows the operator to sense if anything is not quite right before using it.
Remember, cracks in abrasive wheels aren’t always visible to the eye. One way to test for cracks is the ring test. This is where you suspend a wheel from a bore and tap it with a light, non-metallic tool. If a wheel is solid it will emit a clear, metallic ringing.
Personal Protective Equipment (PPE)
As we have already established, PPE should be used as a last resort, after all other control measures have been implemented to manage risks. Employees should be provided with appropriate PPE to protect them against any unavoidable hazards of grinding.
Depending on the type of work and machinery and as determined by your risk assessment, this may include:
- Protective footwear to protect against anything, including the workpiece, being dropped from the machine onto their feet.
- Respiratory protective equipment (RPE) including a face mask to prevent any dust that cannot be removed through ventilation from being inhaled by the operator or those in the vicinity.
- Eye protection to protect against any projectiles, abrasive particles and dust that cannot be prevented using a machine guard, for example when using a portable grinding machine.
- Hearing protection to protect against noise.
- Gloves to improve blood circulation and reduce the risk of HAVs.
- Tight fitting overalls with cuffed sleeves.
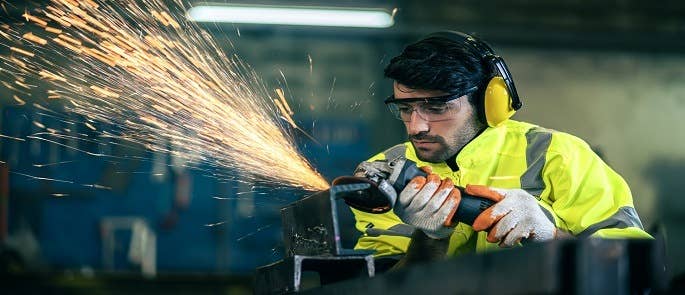
As well as using PPE, there are some things that workers should avoid wearing while grinding, as a safety precaution against being drawn into the grinding machine. These include:
- Long hair untied.
- Long sleeves or loose clothing.
- Things worn around the neck, such as necklaces, ties or scarves.
With the number of potential hazards posed to workers using grinding machinery and abrasive wheels in the workplace, it is essential that you can identify these hazards in your workplace and put the appropriate controls in place to reduce risk. Performing a risk assessment is the best way to certify and maintain the health and safety of workers.
Further Reading
- Ten Common Construction Site Hazards
- RIDDOR: How to Report an Incident or Accident at Work
- 15 Workshop Hazards and How to Avoid Them
- What are the Consequences of Poor Health and Safety Procedures?
- Health and Safety Training for Employees Course