Manual Handling Risk Assessment: Free Template
The most recent HSE statistics tell us that 17% of all workplace accidents are the result of poor handling, lifting or carrying. Manual handling injuries are also amongst the most common in the UK, accounting for around 1 in 5 injuries that last for over 7 days. Many job roles require manual handling activities and, as an employer or responsible person, it’s your duty to ensure they understand how to handle, lift and carry safely through an appropriate risk assessment.
In this article, we’ll outline what a manual handling risk assessment is and why it’s important, what the steps of a manual handling risk assessment are and provide you with a free risk assessment template to use in your workplace.
What is a Manual Handling Risk Assessment?
A manual handling risk assessment is a step-by-step process that enables employers to control the health and safety risks caused by manual handling activities in the workplace.
Under the Management of Health and Safety at Work Regulations 1999, all employers must manage health and safety risks. This means identifying what might cause injury in the workplace, how likely it is someone may be harmed and what can be done to control the risks. Carrying out a risk assessment is the essential first step in this process.
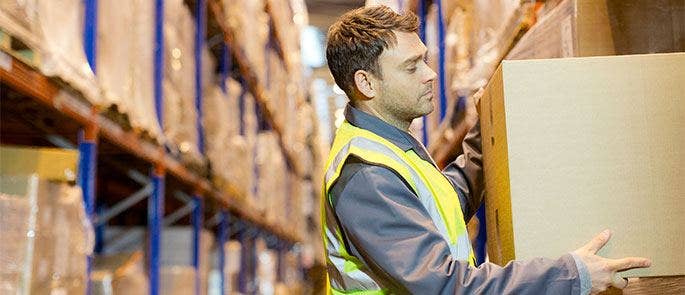
A manual handling risk assessment can be carried out by employers or any competent person nominated by the employer. What’s important is that this person understands the workplace, work activities and manual handling activities carried out there, whether that’s lifting, putting down, pushing, pulling, carrying or moving objects, people or animals.
When carrying out a manual handling risk assessment, the competent person should also keep the TILE acronym in mind: Task, Individual, Load and Environment. When each of these four categories is considered, it will help to more easily identify the manual handling risks that need controlling. You can find out more on TILE in our article: What Does TILE Stand For?
If it’s identified that a risk assessment isn’t enough to control the hazards, either because they cannot be removed or the risk of harm is too great, then a Safe System of Work may need to be considered instead.
What are the Risks of Manual Handling?
The main risks of manual handling are musculoskeletal disorders (MSDs). These are injuries or conditions caused or made worse by poor manual handling practices and can affect the back, neck, shoulders, forearms, wrists, hands, hips, legs, knees, ankles and feet. The HSE estimates that MSDs made up a third of all workplace ill-health conditions.
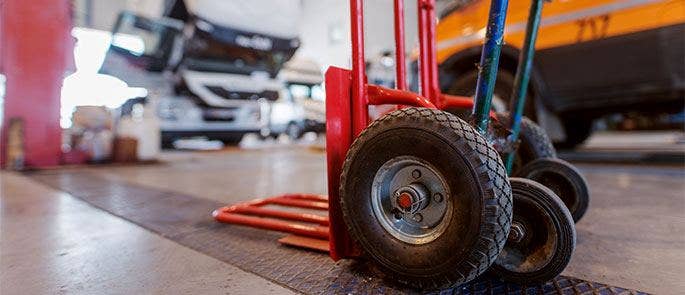
Manual handling makes the risk of developing an MSD more likely if any of the following activities are performed incorrectly or unsafely:
- Bending, crouching or stooping.
- Lifting heavy or bulky loads.
- Pushing, pulling or dragging loads.
- Stretching, twisting and reaching.
- Carrying out repetitive actions.
- Using sustained or excessive force.
- Carrying out a task for a long time
- Working with display screen equipment (DSE).
- Working with hand-held power tools for a long time.
- Driving heavy vehicles, long-distance driving or driving over rough ground.
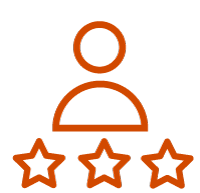
Want to Learn More?
If you have members of staff that carry out manual handling tasks in the course of their work, then training in how to work safely is essential. Our online Manual Handling Course will ensure that your employees are sufficiently trained in the principles and practices of safe manual handling.
5 Steps of a Manual Handling Risk Assessment
There are five steps of a manual handling risk assessment that the competent person needs to follow to ensure their risk assessment is sufficient and effective.
The 5 steps of a manual handling risk assessment are:
Step 1 – Identify the Hazards
This means looking around the workplace, speaking to employees and considering all work activities that involve manual handling and which may cause harm. Take a look at existing ill-health records and accident books to identify any previous issues that have caused harm, too. Then, make a list of each individual hazard you’ve identified.
Step 2 – Who Might be Harmed and How
For each of the identified manual handling hazards, consider who is likely to be harmed by them. It could be workers, visitors, contractors, suppliers or members of the public. Bear in mind that some people have more specific needs because of a disability or their age, for example, so may be at more risk of injury from manual handling than others.
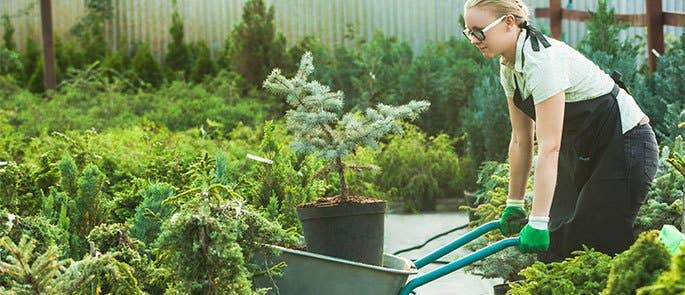
Step 4 – Implement Control Measures
This step means looking at each manual handling hazard and determining what needs to be done to reduce the risk of harm. First of all, the hazard should be removed completely – is there an alternative way the task could be done so manual handling is avoided? If removing the hazard isn’t possible, then how can you control the level of risk? For example, changing the process, introducing machinery, reorganising the workplace or training staff members.
Step 4 – Record Your Findings
For organisations with more than five employees, keeping a record of your risk assessment is a legal requirement. For smaller businesses, it’s not the law but is still recommended. Recording your findings means making a written note of all the identified manual handling hazards, who might be harmed by them and what you are doing to control the risks of harm.
Step 5 – Review and Update
Once your manual handling risk assessment is completed, it’s important that it’s regularly reviewed to ensure the control measures remain effective. There are many reasons why you might need to make changes to the risk assessment, whether it’s because of new staff members, new processes, changes to equipment or something else. The risk assessment should also be reviewed and updated if there have been any related accidents or near misses.
Manual Handling Risk Assessment Template
Below is a free manual handling risk assessment template for you to download and use in your own workplace. Note that all risk assessment templates require personalisation for your own specific workplace and work activities, so you’ll need to check which sections are relevant, add your own and ensure the content is tailored to your own needs.
If manual handling is part of your workplace’s operations, then it’s important to carry out a manual handling risk assessment before allowing employees to begin tasks. The harm caused by incorrect manual handling can be long-term and debilitating for workers, so it’s important that the hazards are identified and control measures put in place to reduce the risk of harm.
Further Resources:
- Manual Handling Online Course
- What are Safe Systems of Work?
- Manual Handling Weight Limits: What are the Safe Lifting Guidelines and Techniques?
- Consequences of Poor Manual Handling