What are Safe Systems of Work?
In every industry there are hazards present that pose a risk to the safety of those in the workplace. Fortunately, many of these hazards can be eliminated through proper control measures, but this is not always possible. When this is the case, employers have a legal and moral duty to protect the health, safety and wellbeing of those in their workplace by implementing safe systems of work.
In this article, we will explain what safe systems of work are, how to design and implement them in your workplace and how they work to reduce the risk of harm, as well as providing some examples of safe systems of work in the workplace.
What are Safe Systems of Work?
A safe system of work (SSoW) is a procedure, or set of procedures, that explains exactly how a work task should be carried out, to make it as safe as possible for the person completing it and those around them. It is a legal requirement for employers and must be put in place whenever a work task involves hazards that cannot be eliminated, thereby posing a risk to the safety of the employee.
SSoWs should be based on the findings of a workplace’s risk assessment. An effective risk assessment identifies the hazards and risks in a workplace and evaluates whether they can be sufficiently controlled through engineering measures, or if a SSoW is required. While SSoWs are not a replacement for the other control measures included in the hierarchy of control, they are necessary when these measures alone do not provide adequate protection from risk.
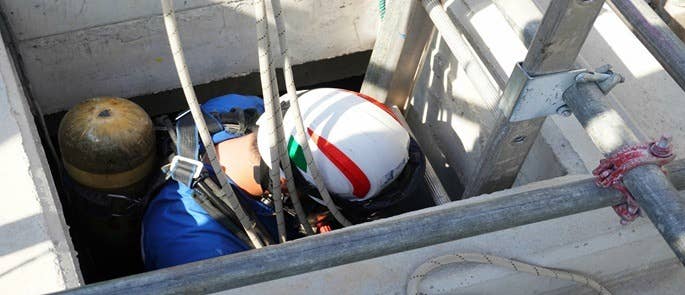
A SSoW should be completed by a competent person, meaning they have the knowledge, training and experience required to understand the nature of the task being considered for a SSoW.
The specific requirements for designing a SSoW will depend on an organisation’s needs and industry regulations. The higher risk the activity being performed, the more detailed a SSoW should be. For very low risk activities, it may be sufficient to distribute a SSoW orally, though it is best practice to have all SSoWs in writing. If a task is particularly high-risk, a permit-to-work may be required.
Safe System of Work vs Permit-to-Work
A permit-to-work is a type of SSoW that allows only certain individuals to carry out a specific task within a defined time frame.
The following work tasks are considered to be high-risk and would therefore require a permit-to-work:
- Hot work.
- Cold work.
- Chemical work.
- Working at height.
- Working in confined spaces.
This list is by no means exhaustive and a competent person is needed to determine whether a task requires a permit to work.
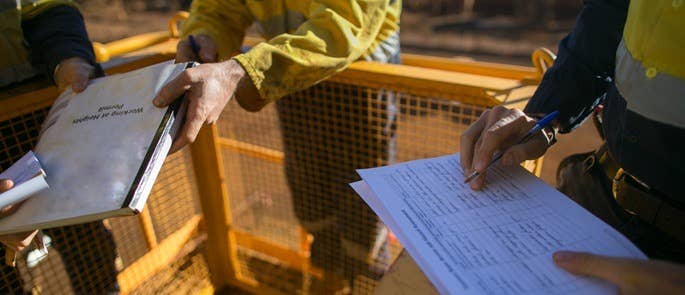
Like a standard SSoW, a permit to work is based on the findings of a risk assessment and establishes the safety precautions needed to carry out a task safely. However, it also requires declarations from a number of individuals, including those authorising the task and those carrying it out. The person carrying out the work must also complete a request form which must then be approved by a competent person.
A permit to work should include:
- The type of work carried out.
- The location of the task.
- Details of the hazards that are present.
- Proposed methods for completing the task safely.
- Who can authorise the task.
- Plant and equipment used.
- Safety precautions required.
- Length of time required to complete the task.
- Conditions that must be met on completion of the task.
- PPE requirements.
Safe System of Work vs Method Statement
A method statement is a written document that sets out the step-by-step process for completing a task safely, as determined by a SSoW. It includes risks identified through the risk assessment and the measures that will be taken to manage those risks. A method statement is intended for use by the person carrying out the task, meaning it should clearly and concisely explain how that task is to be carried out.
A SSoW contains additional information to the method statement that is not required by the person carrying out the task for them to complete it safely. For example, as well as outlining the process for safely carrying out a task and emergency procedures, a SSoW should also include information on the procedures for monitoring and updating the SSoW.
This extraneous information could create confusion in the person carrying out the task and increase the risk of human error. For this reason, the method statement is useful because it only contains information the person completing the task needs to know to be safe.
An effective method statement should outline:
- The location of work.
- A step-by-step description of the work and method to be used.
- Specific hazards relating to the task.
- The plant and/or equipment to be used.
- Control measures, including any PPE required.
- Emergency procedures (including entry and exit procedures).
You should avoid using complicated ‘jargon’ when writing a method statement as it is essential that anyone who may perform the task can read, understand and follow it easily. This reduces the likelihood of misinterpretation or misunderstanding that could lead to harmful errors when completing a task.
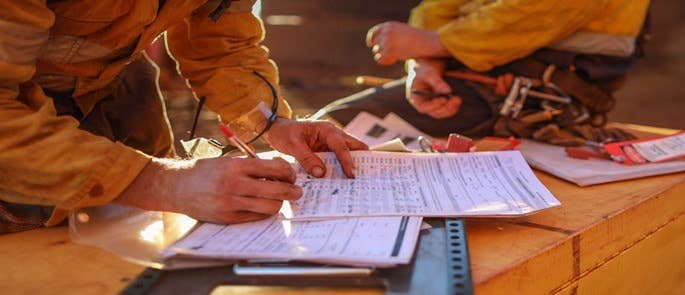
A method statement can be presented in a variety of ways, depending on what best describes the task at hand. Some examples include:
- Step-by-step instructions.
- Decision aids.
- Checklists.
- Diagrams.
- Flow charts.
When deciding on the best format for a method statement, you should consult those who will be completing the task to find out how they prefer to receive information and direction, as they will be the ones using the SSoW and need to understand it. It’s important to monitor whether method statements are actually being used in your workplace and if they aren’t, then they may need to be revised.
Unlike SSoWs, method statements are not a legal requirement for employers. However, because they make SSoWs clearer and more accessible to workers, method statements are a vital tool for ensuring health and safety in the workplace. It is therefore good practice for all SSoWs to be documented in a method statement, though this is particularly important for higher-risk activities.
If you’d like to learn more about method statements, including how to write one, why not check out our article ‘What is a Method Statement and How Do I Fill it in?’ which includes a free, downloadable method statement template.
Safe System of Work Examples
Safe systems of work are used in a number of different industries, particularly those where high-risk work is regularly carried out, such as the construction industry. However, they may also be needed in industries where the hazards are not as obvious, for example in supermarkets or restaurants. For this reason, completing a risk assessment is essential for identifying where SSoWs are needed.
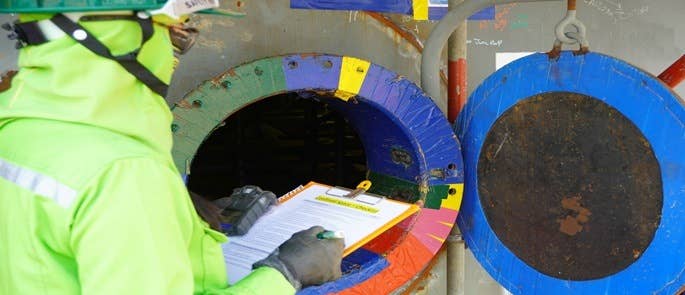
A safe system of work is a combination of physical controls, procedures, plans, training and information that provides a safe work environment or a safe work activity for all employees. For example, SSoWs include:
- Safe Place of Work. The work environment should be safe and not pose risks to health or safety for the work activities that will be undertaken. For example, there should be adequate lighting, access, and ventilation.
- Safe Work Equipment. The safe system of work should include the selection of the most suitable type of work equipment and/or substance by an experienced manager, with the advice of a specialist company where necessary.
- Safe Substances for Use at Work. The safe system of work should only allow the safest substances possible. This may mean substituting dangerous, flammable, or toxic substances, such as chemicals or gases, for safer alternatives.
- Safe Management, Supervision, and Monitoring. Managers, supervisors, those who plan the work, and other duty holders should be competent in their duties. This includes an understanding of the hazards and risks involved with the work activities and work environment, and how to safely supervise and monitor activities.
- Safe Workers. Employees and any others undertaking work activities must be fully trained in the safe system of work, including any work equipment, use of substances, and rescue arrangements. For example, workers are given training before using a dangerous piece of machinery, such as an excavator.
This list is by no means exhaustive. Whenever there is a risk of harm involved in performing a work task, regardless of what that task is or the industry it is taking place in, a safe system of work should be put in place to keep workers safe from harm.
Why Does My Business Need a Safe System of Work?
It is a legal requirement for employers to implement SSoWs in their workplace where there is an unavoidable risk of harm. The Health and Safety at Work, etc Act 1974 requires employers to ensure, as far as is reasonably practicable, the health, safety and welfare of their employees at work. This includes providing and maintaining systems of work that are, as far as is reasonably practicable, safe and without risk to health.
If a high-risk task is performed incorrectly because there is not an effective SSoW in place, this may not only put the person completing the task at risk of harm, but others as well. Under the Management of Health and Safety at Work Regulations 1999, employers are also required to ensure that their activities do not harm the health, safety and welfare of anyone not in their employment that may result from their employees’ work activities, as far as is reasonably practicable.
Employers also have a moral responsibility to ensure safety in their workplace, both to their employees and others in the environment. If an employee is not fully informed on how to perform tasks safely, despite how hard they may try to do so, there is still a significant risk of human error leading to incidents and harm. Employers must do all that they can to provide employees with the tools and information they need to be safe at work.
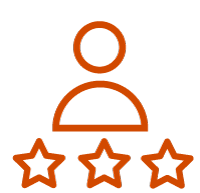
Looking to Learn More?
Safe systems of work are just one of the ways to manage workplace risk. We offer a range of health and safety courses that provide employers and employees with the knowledge required to effectively manage risk by implementing the appropriate control measures for the activity at hand. These include our Control of Substances Hazardous to Health (COSHH) course, our Working at Height course and our Working in Confined Spaces course.
How to Develop a Safe System of Work
There are a number of key requirements for an effective safe system of work. They should:
- Include a brief description of the scope of the task to be undertaken. An effective SSoW should only look at one specific task or activity.
- Identify all potential hazards involved in performing each step of the task, as well as the task as a whole.
- Provide step-by-step instructions for how to complete the task that cover the task from beginning to end.
- Outline the safety measures in place to protect against each hazard identified – for example PPE.
- Be readily available and accessible for anyone who needs them.
When it comes to developing a SSoW for a task, there are a number of key steps involved. These are outlined below.
Step 1: Assessing Tasks and Identifying Hazards
The first step of creating a SSoW is to identify work tasks where the risk of harm cannot be eliminated. This should be achieved by performing a risk assessment of the whole workplace and the activities taking place there.
While a workplace risk assessment should be carried out by a competent person, meaning they have the appropriate knowledge, experience and skills, it is vital that the employees are consulted during this process. As they are the ones most often carrying out the tasks, they are best placed to know exactly how the task is performed and, therefore, what the associated risks are, some of which management may not be aware of or could overlook.
When looking at individual tasks, it can be useful to consider the following:
- The equipment and/or materials used for a task – considering whether the resources used are safe, or if they could be substituted for safer materials.
- Who performs the work – looking out for foreseeable human error that may relate to gaps in knowledge and/or skill.
- Where the task is performed – looking for environmental hazards that may need to be eliminated.
- How the task is performed – looking for risks that may arise in the established process for completing the task, that may require a change in the process.
After assessing each task, with input from the workers, you should be able to recognise the hazards and associated risks involved in performing it. Make a list of all potential hazards involved in each task.
For each task, you should determine:
- Possible causes of harm.
- The likelihood that this harm will occur.
- What safeguarding measures can be taken to reduce the risk of harm as far as is reasonably practicable.
Once the hazards have been identified, you should try to eliminate them as far as possible. A SSoW should not be implemented where a hazard could instead be eliminated or avoided, it should only be used when elimination of the hazard is not reasonably practicable.
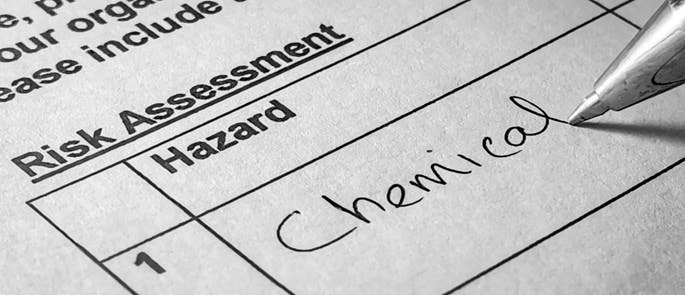
Step 2: Defining Safe Systems of Work
The best way to manage a risk is to eliminate, or, where this is not possible, to substitute the hazard or implement engineering controls to physically protect workers it, effectively removing the hazard. Where none of these can be achieved, and therefore the risk of harm from the hazard can’t be eliminated, safe systems of work must be established to manage this risk as far as is reasonably practicable.
SSoWs are less effective than the other safety measures mentioned above for managing risk because SSoWs do not stop a worker coming into contact with a hazard and its associated risks. However, they are intended to reduce the level of risk posed to workers when interacting with hazards.
A certain task may have a number of possible precautions that could be put in place to make it safer and identifying the most effective can be a challenge. This is why it’s important to consult with your workforce when establishing SSoWs. It’s important to consider which precautions your employees find most practical, as well as what will be most practical to implement logistically and financially. However, you must remember that safety is always the priority.
The process of defining a SSoW includes:
- Determining whether authorisation is required for individuals to perform a task.
- Considering any preparation required to set up the task and conditions that must be ensured.
- Defining a step-by-step procedure for completing the task, including identifying the hazards involved.
- Identifying safe work methods.
- Outlining safe means of entry and exit, including escape, where necessary.
- Considering procedures required after a job is completed, such as dismantling equipment, disposing of dangerous materials or locking machinery.
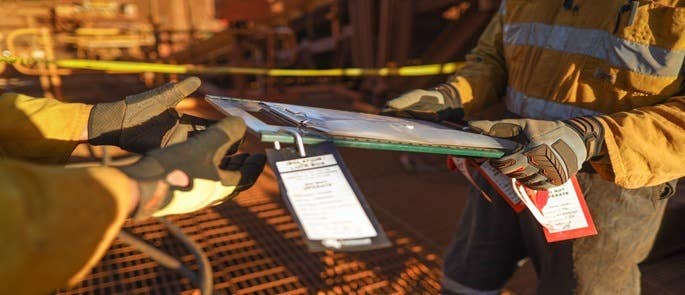
Step 3: Implementing the Safe System of Work
SSoWs cannot be effective safety measures in and of themselves, rather, they need to be understood and implemented fully by those carrying out the work. Some individuals may be tempted to ignore SSoWs if they are overly complex, so it’s essential that they are easy to read and concise, and only containing the key information workers need to know to complete a task safely.
There is no one specific way to introduce and implement a SSoW in your workplace and the process can be formal or informal, depending on the level of risk involved in the task. A formal implementation may involve producing documentation which is then distributed among employees, such as a standard operating procedure (SOP). A less formal implementation may involve putting diagrams next to machinery to explain exactly how it should be used or putting on training for specific processes.
It is good practice to provide employee training every time a new SSoW is introduced to ensure that employees understand it and can implement it effectively. If employees are struggling to understand any part of the SSoW, this also gives you the opportunity to make changes or provide additional upskilling. Any training undertaken by employees in relation to SSoWs should be recorded and competency tests performed where appropriate.
It’s vital that your employees understand why SSoWs are being implemented, otherwise they may be inclined to ignore them or not complete them properly. For this reason, your training may include an explanation of how exactly SSoWs contribute to workplace safety. Toolbox talks are an effective addition to formal training for cementing health and safety knowledge in the construction and trades industry. You can learn more about toolbox talks in our article, here.
It is equally important that your managers and supervisors are trained on SSoW procedures, as they are the ones who will be implementing and maintaining the SSoWs so must understand them fully.
It is also helpful to give each of your SSoWs a unique reference number so that they can be easily written into risk assessments and workers know which SSoW to refer to for specific tasks.
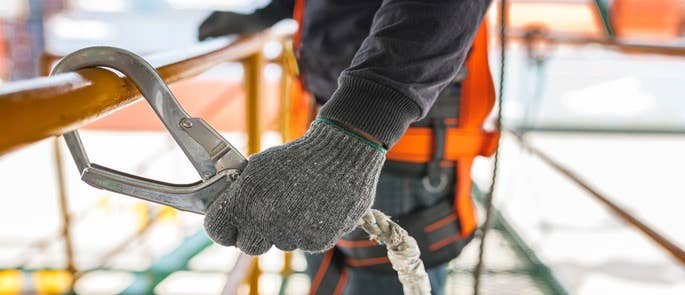
Step 4: Monitoring the Safe System of Work
You should monitor your SSoW as soon as it is implemented to identify whether it is having the intended effect – i.e. managing risks and increasing safety. It’s also vital that this monitoring is continual as, while a SSoW may be effective when it is first implemented,certain factors may cause it to lose effectiveness, meaning it no longer manages risk as it once did.
For example, if you need to introduce a new material to a process due to changes in industry regulations, this may introduce new hazards and associated risks that the existing SSoW is not designed to manage. This would require a change to the SSoW to ensure that it can manage those risks.
Effective monitoring of SSoWs ensures that:
- Employees continue to find the SSoW usable.
- Employees are performing the SSoW properly and it is still effective for managing risk.
- Changes in the nature of the task (or other circumstances) that necessitate a change to the SSoW are identified and implemented as soon as possible.
Particularly when performing a task they do often, employees may be tempted to ignore the SSoW in place for that activity, thinking that they know exactly how to do it already. As well as ensuring employees understand a SSoW, it is also vital that you can ensure they are complying with it, including every step and detail. This is best achieved through a combination of monitoring, regular inspections or checks and supervision.
Monitoring SSoWs allows you to identify when changes need to be made to the SSoW so they can continue to effectively manage risk. The following list outlines some circumstances where changes to SSoWs may be required:
- If a step in the process needs to be changed for any reason.
- When new machinery or equipment is introduced to an organisation and/or process.
- When new materials are introduced or the formulation of a product changes.
- If an accident or incident occurs during work – this indicates that your SSoW is ineffective or that employees are not using it correctly or at all, meaning changes are necessary.
- When there are changes to working patterns or staff involved in a SSoW.
- There are relevant changes to legislation or industry regulations.
Even if a change seems minor, it is important to always consider if it may affect the effectiveness of your SSoWs.
The details of how a SSoW should be monitored and by who should be stated as part of the SSoW documentation, as well as communicated to and understood by the individuals responsible for monitoring.
Having effective safe systems of work in place ensures that employees perform tasks in the safest way possible each and every time. This drastically reduces the risk of accidents and incidents occurring that could lead to harm. Effective safe systems of work, that are regularly maintained and updated, are therefore an essential part of any safe and healthy workplace.
Further Resources:
- How to Conduct a First Aid Needs Assessment: Free Template
- Working in Confined Spaces Hazards and Control Measures
- Electrical Safety Training
- What is ISO 31000 – Risk Management?