What is Lock Out/Tag Out?
There are many risks associated with completing routine maintenance, servicing, repair or inspection of machinery and work equipment. In fact, it’s estimated that maintenance activities cause 25-30% of fatal accidents at work. It is therefore essential that your workplace has sufficient safety procedures in place to mitigate the risks. Lock out/tag out is one of these procedures.
In this article, we will look at what lock out/tag out is, including an explanation of the seven steps involved in the process. We will also examine why lock out/tag out is important and provide guidance on improving the procedure in your workplace.
What is Lock Out/Tag Out?
Lock out/tag out (often referred to as LOTO) is a phrase to describe the safety procedures for the isolation of machinery and other work equipment in which energy is used, stored or created. It’s a system that helps to avoid the potential accidents and incidents that can occur during maintenance, servicing, repair or inspection activities in the workplace.
LOTO involves placing a padlock on a machine once the energy has been fully isolated from it, and then attaching a tag to the machine to communicate that it should not be used. This ensures that workers can complete necessary maintenance, servicing, repair or inspection work safely, without putting themselves or others at risk.
It is also used for machines that present risks during maintenance, servicing, repair or inspection. For example: power presses, processing machines and automatic processing lines, mixing machines, ovens, conveyor systems, mechanical handling systems and process lines, amongst others.
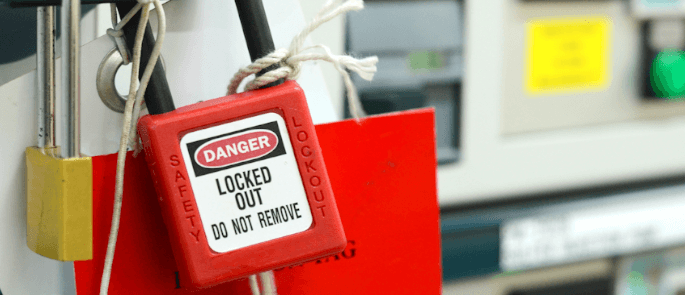
Risk assessment and the hierarchy of control
Lock out/tag out is an administrative step on the hierarchy of control. LOTO is a part of the risk assessment and part of a safe system of work (SSoW).
The Management of Health and Safety at Work Regulations 1999 (MHSWR) requires all employers to conduct risk assessments for their work activities and locations.
To do a risk assessment, you need to take the following five steps:
- Step 1: Identify the potential hazards in your workplace and from your work activities.
- Step 2: Think about who might be harmed and how – not just employees but also contractors, visitors and members of the public
- Step 3: Evaluate the risks and implement controls. This involves deciding how likely it is that the hazards will cause risk to health and safety and what to do about it.
- Step 4: Record your findings. This is a legal requirement if you employ five or more people, but it is good practice for any workplace and activities there.
- Step 5: Regularly review your risk assessment as things change, such as new or altered processes or new employees.
It’s important to remember that LOTO as a process is not a substitute for a risk assessment.
The hierarchy of control is intrinsic to a risk assessment. It is a five-level structure that helps employers and duty holders understand the order in which precautions should be applied to control the risks associated with their work activities.
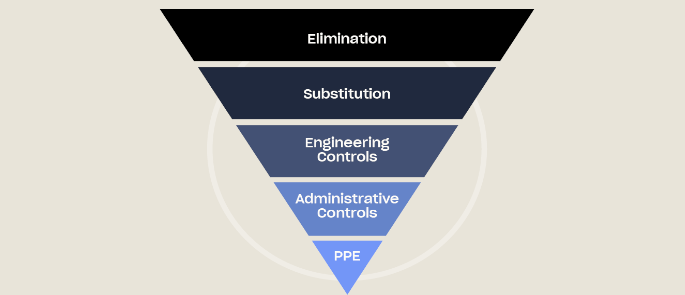
The hierarchy starts with the most effective controls at the top of the structure, descending to the least effective. When considering selecting controls for your work activities, they must be adopted in the order outlined below:
- Elimination.
- Substitution.
- Engineering controls.
- Administrative controls.
- PPE.
As mentioned previously, LOTO is an administrative step on the hierarchy of control and part of a safe system of work. We will explore what this means below.
Safe systems of work (SSoW)
Once elimination, substitution, and engineering controls have been considered to manage risks, under the hierarchy of control, administrative controls can be used to reduce any remaining risks.
Administrative controls include enforcing safe systems of work (SSoW) and ensuring employees are provided with the necessary information, instruction, and training. LOTO is one example of an administrative control.
A safe system of work is a combination of physical controls, procedures, plans, training and information that provides a safe work environment or a safe work activity for all employees.
The key information contained within a safe system of work is:
- Safe Place of Work. The work environment should be safe and not pose risks to health or safety for the work activities that will be undertaken. For example, there should be adequate lighting, access, and ventilation.
- Safe Work Equipment. The safe system of work should include the selection of the most suitable type of work equipment and/or substance by an experienced manager, with the advice of a specialist company where necessary.
- Safe Substances for Use at Work. The safe system of work should only allow the safest substances possible. This may mean substituting dangerous, flammable, or toxic substances, such as chemicals or gases, for safer alternatives.
- Safe Management, Supervision, and Monitoring. Managers, supervisors, those who plan the work, and other duty holders should be competent in their duties. This includes an understanding of the hazards and risks involved with the work activities and work environment, and how to safely supervise and monitor activities.
- Safe Workers. Employees and any others undertaking work activities must be fully trained in the safe system of work, including any work equipment, use of substances, and rescue arrangements.
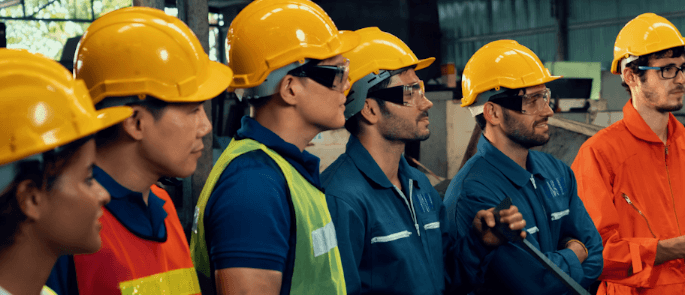
The Seven Steps of LOTO
There are a number of critical steps to a LOTO procedure. These are a logical series of actions that ensure all the steps of LOTO are completed. Almost all LOTO procedures fall into this series of steps, which we have listed below.
- Step 1: Preparation – This involves identifying the energy sources and control devices of the machine in question – for example, how is the machine powered? Electricity is the most commonly used energy source; however, some machinery is powered by hydraulic or pneumatic energy.
- Step 2: Initial Information and Training – It’s crucial to ensure that everyone who needs to know that the work equipment will be under maintenance, serviced, repair or inspection are fully informed beforehand. This includes not only employees who usually work on or nearby the machine, but others such as contractors or cleaning staff that work in the vicinity.
- Step 3: Initial Isolation of Work Equipment – All forms of energy need to be fully isolated from the work equipment. The first step here is to switch off the stop button on the machine – which doesn’t isolate the equipment. That needs to be done separately, usually by moving the isolator switch for the equipment to ‘off’.
- Step 4: LOTO – Lock Out of Work Equipment – Now that the machine’s isolator has been switched off, it should be locked with a padlock. Typically there are two holes in the isolator handle or the isolator switch in the main control panel. Once these holes are aligned, a padlock can be fitted and locked. Usually, the person who locks off the equipment also retains the key.
- Step 5: LOTO – Tagging and Testing – As soon as the padlock has been fitted, the person doing the work should also fit a “lock out warning tag”. This tag should be able to be attached securely to either the padlock or the machine, and must contain a warning label. It should also have the space to write the name of the person who has fitted it.
- Step 6: Communication During the Work – It’s essential, for the safety of everyone involved, that there are clear lines of communication throughout the maintenance, service, repair or inspection work. Voice communication is often sufficient, however, if the maintenance takes place in an enclosed space, for example, or an area with low-light, it might be necessary to use a radio or another wireless system.
- Step 7: Completion of Work and Return to Service – Before the work equipment is released for normal service, a manager or supervisor must confirm that the work has been completed and the equipment is in a safe condition. It’s vital that the lock out devices and tags are removed by the same person who fitted them.
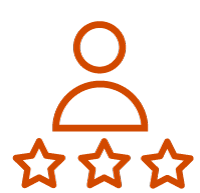
Want to Learn More?
Our Lock Out/Tag Out course outlines the health and safety hazards and risks that LOTO helps to control, and how the principles of LOTO should be applied to risk assessments.
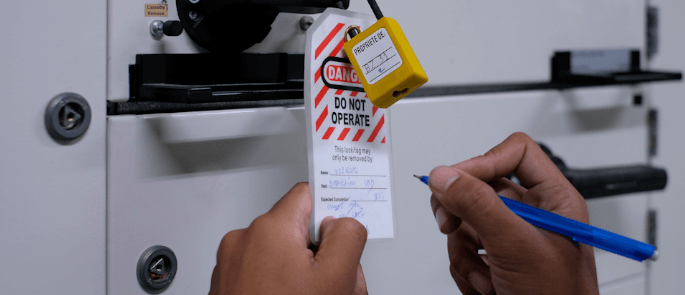
Why is LOTO Important?
Lock out/tag out is a safety process that helps to safeguard employees against hazards and risks that they, and other people in the vicinity, can be exposed to while routine maintenance is carried out.
These include, but are not limited to:
- Moving parts of machinery. This can cause entrapment, crushing and/or amputation of parts of the body. Examples include the tools of machinery, moving parts of plant such as rotating blades in fans, mixers of tanks or drums or conveyor systems.
- Electrical risks. As we’ve explained, electricity is the most commonly used energy source, and this presents its own risks. For example, electric conductors, which are assumed ‘dead’ and are exposed for work on them may become live and cause electric shock or burns.
- Falls from height. It’s common for maintenance work to involve working on roofs, gutters and building services. Equally, it may involve needing to reach raised sections of machinery or work equipment. These activities would involve using access equipment. For more information on controlling working at height hazards, check out our article, here.
- Falls of heavy objects. Heavy items sometimes have to be moved or are disturbed during maintenance work – for example, access covers or disconnected parts.
- Disturbing asbestos. Many older plant and machinery items still contain asbestos products, for example, gaskets, filters and other parts. There is also asbestos-containing material in parts of older buildings and structures, for instance, sprayed asbestos coating on steelwork and pipes, lagging, and asbestos insulation boards. For more information on asbestos, check out our article.
Legal Requirements
There are a number of Regulations under health and safety law that must be complied with that relate to LOTO. We have explained some of the key legislation below.
Under the Health and Safety at Work etc Act 1974, employers must ensure, so far as is reasonably practicable, their employees’ health, safety and welfare whilst at work. This is a wide-ranging duty and encompasses preventing and controlling risks that may result from maintenance, servicing, repair or inspection work. This includes ensuring the proper planning, organisation, control, monitoring and review of preventative and protective measures.
The Management of Health and Safety at Work Regulations (MHSWR) 1999 also applies to all work activities and places additional legal duties on employers to manage health and safety in the workplace.
One of the key duties under MHSWR is to ensure that a risk assessment is regularly carried out and the findings are recorded.
Under both the HSW Act and MHSWR, employees also have responsibilities to work safely and in accordance with any training and information given to them and to immediately report any health and safety concerns to their employer or manager.
The Provision and Use of Work Equipment Regulations (PUWER) 1998 apply to a wide range of work equipment across all types of work activities, and are therefore relevant to LOTO procedures, too.
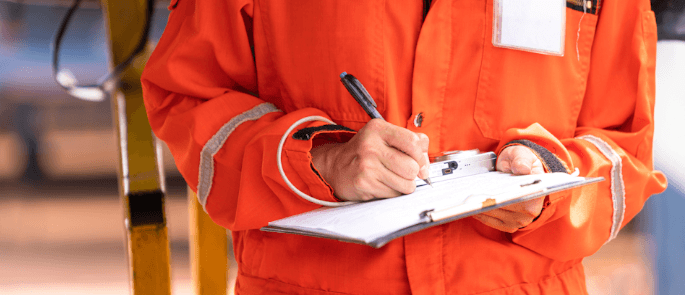
How to Improve LOTO Safety
There are certain ways that employers can help to improve the safety of a LOTO procedure, including ensuring that inspections are carried out and that all employees are fully trained. We’ll look at these in more detail below.
LOTO Inspections
If your workplace uses LOTO procedures, there should be an inspection conducted at least once every 12 months to evaluate the current system in place.
The inspection must be conducted by a competent person. There must also be a second person involved, who carries out the LOTO procedure. The person carrying out the inspection cannot be the one carrying out the procedure.
A LOTO inspection must determine whether:
- Employees are aware of, and fully understand, their responsibilities regarding how to conduct a LOTO procedure safely.
- Each step of the LOTO procedure is being followed – including, for example, whether everyone involved is being informed of the upcoming maintenance and whether they each understand what the different types of lock out/tag out devices, such as padlocks or tags, mean.
- The overall success of the current system in place.
The results of the inspection will highlight any deficiencies with the current system and controls should then be implemented to improve or make changes to the process – such as offering further training to employees – if the results show a need for improvement.
LOTO Training
Employers must provide LOTO training and having employees complete lock out/tag out training has many benefits. A training course outlines the hazards and risks associated with maintenance work in detail, highlighting the importance of using a LOTO procedure to protect employees from these.
It also explores each step of the risk assessment process in detail, and explains how it links with the hierarchy of control and safe systems of work.
A LOTO training course will also outline the seven steps of a LOTO procedure, and goes into detail about what is required at each step. It also describes the role and responsibilities of those involved in LOTO.
Take a look at our Lock Out/Tag Out Training course which is suitable for workers at all levels, who are involved in lock out/tag out procedures to complete routine maintenance, service, repair or inspection of work equipment.
However, it’s crucial to understand that a lock out/tag out training course must accompany practical training and be a part of general health and safety training. It is not a substitute. Completing an online course does not provide any assurances of being deemed competent to carry out procedures such as LOTO. Instead, it provides awareness and theoretical knowledge of the procedure.
We hope you’ve found this article on lock out/tag out informative and helpful. If you have any further questions about the topics discussed in this article, don’t hesitate to get in touch with us at High Speed Training. You can contact our friendly team on 0333 006 7000 or email support@highspeedtraining.co.uk.
Further Resources
- Online Health & Safety Courses
- Understanding DSEAR – Area Classification & Hazardous Substances
- What is a Safety Data Sheet?