What is a Safety Data Sheet?
Under the Control of Substances Hazardous to Health (COSHH) Regulations 2002, employers have a duty to ensure the risks posed by hazardous substances are either eliminated or suitably controlled. To do this, they need to carry out a risk assessment of the hazardous substances that their work uses or generates. This includes any chemical products.
Chemical products come with safety data sheets, which provide comprehensive safety information about the product. For employers, these help to inform (but not replace) the risk assessment process, as they contain guidance on the risks that the chemical poses and advice on suitable control measures. All this information plays a part in helping employers identify what they need to do to control the risks. For example, by advising how the chemical must be stored.
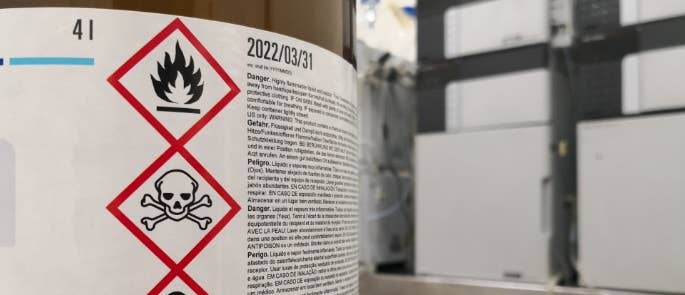
This article explains the purpose of safety data sheets, what products require them, and who is responsible for providing them with chemical products. It also offers guidance on how employers should use safety data sheets. Finally, we’ll look at a safety data sheet example, so you can see what one typically looks like.
The topics covered in this article include the following:
- What is a Safety Data Sheet?
- What is the Purpose of a Safety Data Sheet?
- Safety Data Sheets and Employers
- Safety Data Sheets and Employees
- What Products Require a Safety Data Sheet?
- Who is Responsible for Providing Safety Data Sheets and When are Safety Data Sheets Supplied?
- What About Updating Safety Data Sheets?
- Safety Data Sheet Example and Guidance on How Information is Communicated
- Where to Find Additional Guidance on Safety Data Sheets
Use the above links to jump to that section of the article.
What is a Safety Data Sheet?
Under the UK Registration, Evaluation, Authorisation and Restriction of Chemicals (UK REACH) Regulations, manufacturers and suppliers of chemicals must provide safety data sheets (SDS), free of charge, with their products. This applies to almost all chemical products that are placed on the market.
A safety data sheet provides important information about the chemical:
- Identification of the substance or mixture.
- The name, address, and contact details of the manufacturer or supplier.
- Hazard identification of the chemical(s) in the substance, including hazards caused by reaction with any other substances.
- Composition details and information on ingredients, including the physical and chemical properties, stability, and reactivity.
- Toxicological information, including routes of entry to the body (inhalation, ingestion, skin or eye contact, or other routes), the symptoms of exposure, and exposure controls.
- Ecological information, including toxicity, persistence and degradability, bioaccumulation potential, and mobility in soil.
- Accidental release measures, including personal precautions and emergency procedures, environmental precautions, and methods and materials for containment and clean up.
- Safe transport, handling, storage, and disposal information, including any incompatibilities and any conditions to avoid.
- Exposure limits, including occupational exposure limit values and information on monitoring procedures.
- Regulatory information, including any safety, health, and environmental regulations and legislation that is specific for the substance or mixture.
- Personal protection, such as when eye or face protection, skin protection, or respiratory protection is required.
- First aid procedures, including any immediate medical attention and special treatment that may be needed.
- Fire-fighting measures, including how to suitably extinguish a fire involving the chemical and any special hazards that could arise, such as toxic fumes.
All of this information in the safety data sheet is produced by the manufacturer, and suppliers must provide the sheet with the product. As mentioned earlier, this is legally required under the UK REACH Regulations.
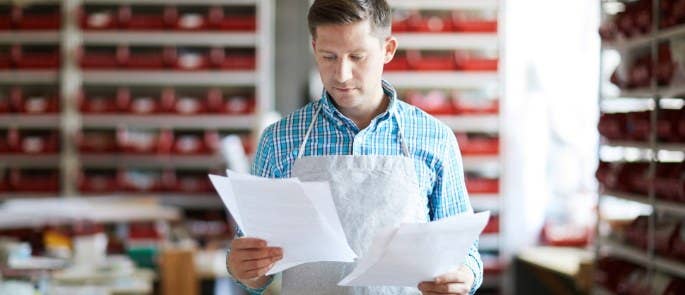
It’s worth noting that safety data sheets were previously known as material safety data sheets (MSDS), but this name was changed to safety data sheets (SDS) in 2015. If you see them referred to as material safety data sheets anywhere, they are using the old name for safety data sheets.
What is the Purpose of a Safety Data Sheet?
A safety data sheet’s purpose is to provide comprehensive safety guidance about the chemical product. All of this information will help guide employers in identifying how to suitably control the risks posed by the chemical.
It’s crucial to note, however, that safety data sheets are not substitutes for risk assessments. Rather, they help to inform the assessment. This is because safety data sheets are not specific to a workplace and do not set out the controls needed for it. The circumstances of the premises, how the chemical is used, and other various factors all play a part in determining what controls are needed. The guidance in the safety data sheet should be used or adapted where relevant to these factors.
Safety data sheets can also assist in the employer’s duty to provide workers with information, instruction, and training where necessary. Employers must inform workers of the risks posed by hazardous substances and what they are doing to control them.
Let’s go into more detail about the purpose of safety data sheets in the context of both employers and employees.
Safety Data Sheets and Employers
The employer, or competent person who has been delegated the duty of carrying out the risk assessment, needs to consider the important information in the safety data sheet alongside specific details of their organisation. This includes how the chemical will be used, where it’ll be used, and who will use it in their business.
For example, they should consult the information about how the chemical should be stored, then assess if there is a suitable location on their premises. Likewise, they should look at the hazards that the chemical poses, consider who will be using them, and then determine how to protect those people from the hazards. This may include engineering controls like local exhaust ventilation to remove fumes from the air, for instance.
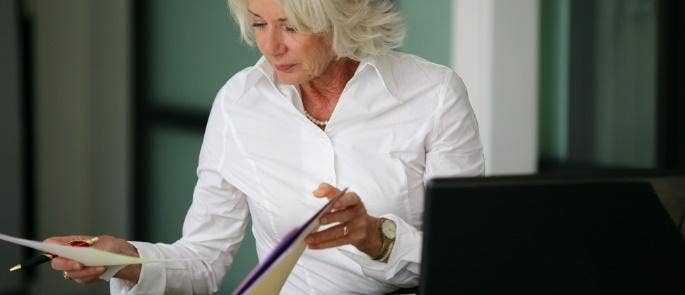
The measures required after reviewing the safety data sheet depend on the specific circumstances of the business and how the product is used. This is why it’s so important to not consider it a substitute for risk assessment.
All the information that is relevant to the particular use or production of the substance should be taken from the safety data sheet and added to the risk assessment. This will help to inform the control measures, safe systems of work, and instructions, training, and information provided to users.
Safety Data Sheets and Employees
COSHH has specific requirements in relation to employers providing information, instruction, and training where necessary regarding hazardous substances. This will ensure that employees can fulfil their responsibility of properly using control measures and facilities.
Safety data sheets can form part of the information, instruction, and training that the employer provides to their workers. However, it is not sufficient for employers to only provide a safety data sheet. The controls for all hazardous substances in the workplace must be clearly explained and all the information provided in an understandable format.
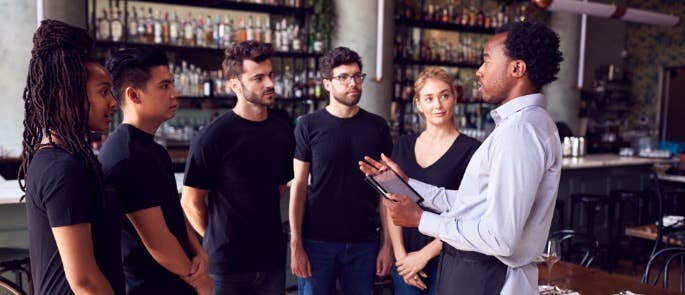
Guidance on COSHH states that employers could distil the information from safety data sheets to give to employees, so they can understand them in the context of the chemical substances they work with or around. This will ensure they receive the information that is relevant to them and is comprehensible. Otherwise, safety data sheets contain a lot of complex information that may make things more confusing for workers.
If employees do want to see safety data sheets, however, then they should receive access to them. In that case, the employer should ensure employees understand that safety data sheets are a part of the overall risk assessment, not a substitution, which must be followed first and foremost.
What Products Require a Safety Data Sheet?
The UK Registration, Evaluation, Authorisation and Restriction of Chemicals (UK REACH) Regulations state that safety data sheets are required if the product meets the following criteria:
- Where a substance or mixture meets the criteria for classification as hazardous in accordance with Regulation (EC) No 1272/2008; or
- Where a substance is persistent, bioaccumulative and toxic or very persistent and very bioaccumulative in accordance with the criteria set out in Annex XIII; or
- Where a substance is included in the list established in accordance with Article 59(1) for reasons other than those referred to in points (a) and (b).
Safety data sheets are therefore required for a very broad range of chemical products. Any chemical that presents a physical or health hazard requires one. In the context of business use, this means employers must receive a safety data sheet for any hazardous chemical products they purchase and that are involved in their business activities.
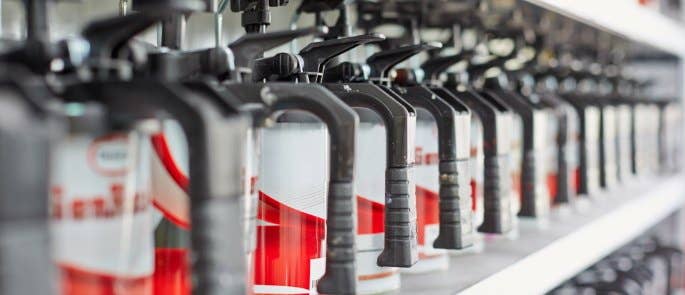
The UK REACH Regulations also state that:
“The safety data sheet need not be supplied where hazardous substances or mixtures offered or sold to the general public are provided with sufficient information to enable users to take the necessary measures as regards the protection of human health, safety and the environment, unless requested by a downstream user or distributor.”
This means that the general public who purchase chemical products don’t need to be supplied with a safety data sheet. However, the safety data sheet will still exist, and must be referred to by employers when the product will be used in a work context.
It’s also important to note that hazardous substances which are generated as part of work activities don’t have safety data sheets, such as fumes created by welding or hazardous dust created by woodworking. Information about these, which are important to cover in the risk assessment, will therefore have to be sought from other sources. For example, from Health and Safety Executive (HSE) guidance online or in the manufacturer instructions of equipment.
Who is Responsible for Providing Safety Data Sheets and When Are Safety Data Sheets Supplied?
The ultimate responsibility of producing and making safety data sheets available rests with the manufacturer of the product.
They must also ensure that suppliers have access to these and can pass them onto employers. Suppliers must provide safety data sheets to employers who purchase the product. They can do so when they buy the product or on request.
Employers must refer to safety data sheets for their chemical products to help inform the risk assessment. As discussed in the previous section, they may also make the information from the safety data sheets available to employees by distilling the contents into all the relevant details they need to know, in a more comprehensible format.
What About Updating Safety Data Sheets?
Manufacturers and suppliers must update safety data sheets:
- As soon as new information which may affect the risk management measures, or new information on hazards becomes available;
- Once an authorisation has been granted or refused;
- Once a restriction has been imposed.
Employers should check annually with manufacturers or suppliers that their safety data sheets are up to date. If there’s a new version, they should obtain and refer to it instead of the old version. This may mean carrying out a new risk assessment if there are changes that impact it. They should archive old copies.
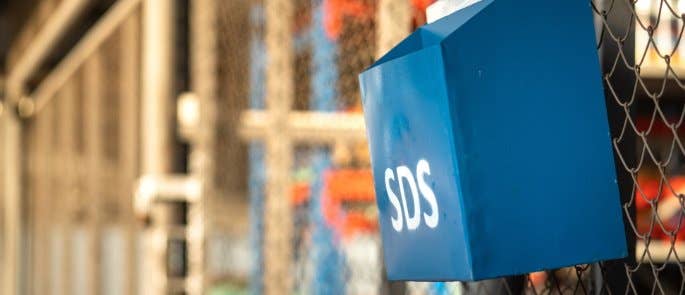
Safety Data Sheet Example and Guidance on How Information is Communicated
Below is a safety data sheet example. This will provide you with an idea of what they look like if you haven’t seen one before.
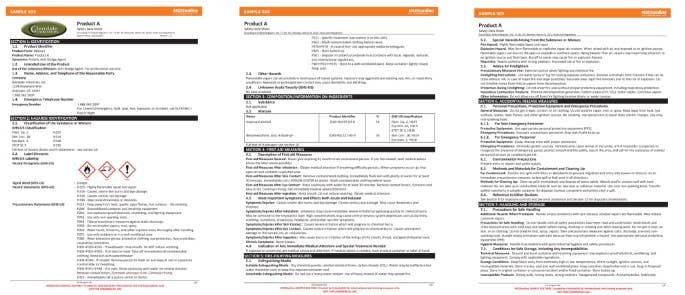
Earlier in this article, we listed all the sections that are contained in a safety data sheet. Alongside the above example pages, that list will give you a good breakdown of what a safety data sheet covers and the information that employers can use to help inform their risk assessment.
As discussed earlier though, it’s important for these sections to be read in the context of how the product will specifically be used by the business. It’s therefore difficult to provide specific advice on how to interpret safety data sheets.
However, here is some guidance on how safety data sheets communicate information that will help with interpreting it:
- Hazard statements. These are phrases that describe the nature of the hazards that the substance or mixture poses. For example, “causes serious eye damage”, “toxic if swallowed”, “toxic to aquatic life with long lasting effects”, or “may cause allergy or asthma symptoms or breathing difficulties if inhaled”.
- Precautionary statements. These describe the recommended control measures for minimising or preventing the adverse effects that can result from exposure to a substance or mixture, e.g. due to its use or disposal. Examples include “wear eye protection”, “do not eat, drink, or smoke when using this product”, “avoid release to the environment”, and “in case of inadequate ventilation, wear respiratory protection”.
- Signal words. The two signal words are “Danger” and “Warning”. “Danger” is used for chemicals with more severe hazards, while “Warning” is used for less severe hazards.
If the employer or competent person referring to the safety data sheet needs help interpreting any of the information, it may be useful for them to contact the supplier or manufacturer, whose contact details will be on the sheet.
Where to Find Additional Guidance on Safety Data Sheets
This article has covered the fundamentals of safety data sheets, including what a safety data sheet is, what their purpose is, what products require a safety data sheet, and more. However, if you’d like further guidance about them, you can visit the following pages:
- The UK Registration, Evaluation, Authorisation and Restriction of Chemicals (REACH) Regulations
- Guidance on the Compilation of Safety Data Sheets – European Chemicals Agency (ECHA)
- UK REACH – the Health and Safety Executive (HSE)
- COSHH Frequently Asked Questions – the HSE
Safety data sheets are important for helping employers carry out a risk assessment of chemical products, though it’s important to remember they are not a substitute for the assessment. They are produced by manufacturers and contain key information about the product, including identification of the substance, composition details, toxicological information, guidance on transport and storage, and more. This must all be considered alongside the specific details of how the product is used in the business, to help the employer identify how to eliminate or control the risks.
What to Read Next:
- Control of Substances Hazardous to Health (COSHH) Training Course
- How to Safely Store, Handle & Dispose of Corrosive Chemicals
- COSHH – A Guide to Employers’ and Employees’ Responsibilities
- Health and Safety in a Bakery: Free Checklist
- Welding Hazards in the Workplace: Safety Tips & Precautions