What is Hot Work and Do I Need a Permit?
Hot work can create significant health and safety hazards that put workers, those around them, and the premises itself in danger.
Employers have a legal duty to ensure that risks in their workplace are assessed, controlled and monitored so that their employees remain safe from harm – including those from hot work. Employers must identify the hazards in their workplace and implement suitable controls to reduce the risks to as low as is reasonably practicable.
What is Hot Work?
The HSE defines hot work as the: ‘use of open fires, flames and work involving the application of heat by means of tools or equipment.’ Common types of hot work include:
- Welding, brazing, and soldering.
- Grinding and cutting.
- Thawing pipes.
- The use of open flames, blow-lamps, and torches.
- Using bitumen and tar boilers.
- The use of hot air blowers and lead heaters.
This is not an exhaustive list, but it does include the most common examples of hot work. All hot work can pose significant health and safety risks when carried out without proper controls.
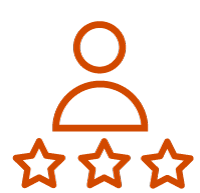
Want to Learn More?
Our Hot Work course examines the different types of hot work and the risks associated with them. It also explains the legal duties on employers and duty holders, and the responsibilities employees have to ensure their safety and the safety of others.
Common Hazards of Hot Work
Hot work can present numerous types of hazards to workers and the environment around them. However, the most common and significant risk of hot work is fire and explosions. Without the proper safety procedures, all types of hot work can easily ignite a fire.
Fire hazards posed by hot work include:
- Flying sparks. This is the main risk posed by hot work. Sparks can easily get trapped in cracks, pipes, gaps, holes, and other small openings, where it will potentially smoulder and start a fire.
- Flammable swarf, molten metals, slag, cinder, and filings. The debris and residue that hot work creates are often highly combustible and/or hot.
- Heat conduction when working on pipes. Hot work can cause a pipe to heat up substantially and this heat can easily transfer through the process of conduction to another, potentially flammable surface and cause a fire.
- Hot surfaces. If you don’t properly remove flammable materials or substances from the area before you start hot work, they could come into contact with a surface that has become hot during the work and easily start a fire.
- Explosive atmospheres. In certain environments, there may be vapours or gases in the air that are highly combustible and could ignite when exposed to hot work. Similarly, the hot work could generate fumes that create an explosive atmosphere.
The consequences of these hazards can be severe and costly for any business. Injuries can result in workers taking time off work, while a serious fire could damage the building irreparably. Both of these could even lead to legal consequences under certain circumstances. Therefore, it’s crucial to understand how to implement appropriate safety controls.
Further hazards include, but are not limited to, the following:
- Exposure to fumes and gases: Hot work can expose workers to hazardous fumes and gases that can result in severe health and safety impacts. This exposure may be a direct result of the hot work activity, such as welding fumes, or a result of the environment where the hot work is being undertaken. For example, carrying out hot work to repair a silo without proper removal of previous residues could result in serious adverse reactions, such as generating toxic fumes or an explosive atmosphere.
- Exposure to electrical hazards: Depending on the type of hot work being undertaken, live electrical circuits may be used to generate heat, which results in a risk of electric shock.
- Heat exposure: Hot work involves ‘use of open fires, flames and work involving the application of heat’, which can expose workers to dangerous elevated temperatures and heat build-up in the body. Excessive heat exposure can result in heat stress, heat stroke and unconsciousness.
- Exposure to improper isolation of equipment: Improper isolation of equipment being worked on can result in hazards including entrapment, crushing, asphyxiation, explosive environments, etc. For example, failure to correctly chocking moving equipment is in place or not isolating pipework that could carry gases, vapours or fumes into the workplace.
It’s important to note that the hazards associated with hot work will depend on the specific work activity and the environment in which it is being undertaken.
Hot Work Control Measures
A variety of industries may require hot work in their premises as part of routine work activities, though it is also frequently carried out as part of contractual work. However, no matter the reason for, or duration of, the hot work being undertaken, it’s essential that the hazards have been assessed and appropriate controls have been enforced.
As previously mentioned, employers have a legal duty to ensure that risks in their workplace are assessed, controlled and monitored so that their employees remain safe from harm, including the risks from hot work activities. Control methods must be selected in line with the hierarchy of control which is outlined below:
- Elimination – Elimination means to avoid carrying out hot work activities. This can be done through a number of ways. For example, if a tank requires hot work to repair it, completely replacing the tank instead of repairing it.
- Substitution – The second step in the hierarchy involves substituting for a safer or less hazardous alternative, such as using cold cutting or cold repair methods rather than hot work.
- Engineering controls – This involves using physical solutions to reduce risks, such as using general mechanical ventilation (ducted air with fans) or local exhaust ventilation (to remove fumes from the point of origin).
- Administrative controls – This involves altering the way the activity is undertaken to make it safer, e.g. the use of safe systems of work, permit-to-work systems and training.
- Personal Protective Equipment (PPE) – The final stage of the hierarchy of control is the use of PPE to reduce any residual risks. Examples of PPE include respiratory protective equipment (RPE), hearing protection, eye protection and anti-static clothing and boots. PPE must only ever be used as a last resort and only when all other stages in the hierarchy of control have been considered.
Avoiding hot work altogether
Hot work must be avoided, so far as is reasonably practicable. ‘So far as is reasonably practicable’ means that, for any risk that is more than negligible or insignificant, then the duty holder has to weigh the risk against the time, money and trouble required to control it. The level of action should be proportionate to the risk. So, where risks are higher, such as hot work, then the actions taken must be more comprehensive. Therefore, you should consider every possible alternative for completing a task before deciding to proceed with hot work.
The need for hot work can be eliminated or substituted for safer alternatives in many ways. For example, replacing tanks and silos instead of repairing them, substituting welding for bolting methods, or substituting torch cutting for the use of hand-held hydraulic shears.
In some situations, hot work will be unavoidable. If this is the case, the duty holder must ensure that an effective safe system of work is enforced and used, to ensure that the work activity will be carried out safely and without risk to health.
Safe systems of work (SSoW)
Safe systems of work are part of the risk assessment process. The information contained within an SSoW should reflect and build on the information developed in the risk assessment process. The key information contained in a safe system of work are outlined below:
- Safe Place of Work – The work environment should be safe for the work activities to be undertaken.
- Safe Work Equipment – The safe system of work should only permit the use of the safest work equipment possible.
- Safe Substances for Use at Work – The safe system of work should only allow the safest substances possible. This may mean substituting dangerous, flammable or toxic substances such as chemicals or gases for safer alternatives.
- Safe Management, Supervision and Monitoring – Managers, supervisors, those who plan the work, and other duty holders should be competent in their duties. This includes an understanding of the hazards and risks involved with the work activities and work environment, and how to safely supervise and monitor activities.
- Safe Workers – Employees and any others undertaking work activities must be fully trained in the safe system of work, including any work equipment and use of substances, and in rescue arrangements.
What is a permit-to-work?
A permit-to-work system is a written procedure to ensure that specific work activities are adhered to. Key information about permit-to-work systems is outlined below:
- A permit-to-work is a document created to control and communicate the key control measures that are needed for work activities where hazards are increased due to the work to be undertaken or by the nature of the location where the work is being carried out. Permits-to-work form part of the safe system of work for those more hazardous work activities.
- The main purposes of a permit-to-work is to act as a single communication tool for a specific and time-bound activity that can cause increased hazards and risks if the additional controls and checks are not included.
- A permit-to-work is a formal written system that makes up part of the risk assessment process and contributes to the safe system of work. It is not a replacement for either of them.
- Only a competent person in a position of authority, for example, a senior manager, can decide whether a permit-to-work is required.
- Where a permit-to-work is needed, it must only be completed by a competent person in authority, such as an experienced supervisor, consulting specialist advice where necessary, and must be signed off by the competent person in charge of the work. The permit-to-work is a suitable way to record authorisations, document findings, and to permit work to proceed.
- A permit-to-work must be specific to the work being carried out and the environment where it is being undertaken. Once the work activity has been finished, the permit-to-work must be cancelled in writing by the senior manager and supervisor, and a new assessment undertaken for any new work activities.
- Anyone carrying out work must be fully informed and instructed in the risk assessment, safe systems of work and the permit-to-work before any work is carried out.
It is essential to note that a permit-to-work, alone, does not make a work activity safe. It is an extension of the safe system of work and must not be used as a replacement.
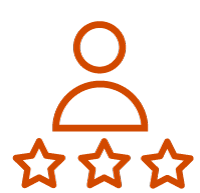
Need Permit to Work Training?
Our Permit to Work Training explains the duties of everyone responsible for the permit, from the point of issue to the work’s completion. If you work in an industry that often carries out high risk work, it’s crucial that you know what a permit should cover.
What information does a permit-to-work cover?
As previously mentioned, a permit-to-work system is a written procedure to ensure that specific work activities are adhered to. A permit-to-work will usually contain the following information:
- Permit title.
- Permit reference, including other relevant permits to work.
- Job location. This must include a clear and accurate description of the area in which the work will be undertaken.
- Date and duration of permit. It’s important to note that a new permit will normally be required for different work shifts.
- Plant or equipment to be worked on. This should include the specific identification number or location where the work will be undertaken.
- Description of work to be done. This section should include sufficient detail to clearly identify the work being done.
- Hazard identification, including detailed information on the hazards arising from the work and other associated hazards, for example, work at height.
- Precautions required, for example, safe equipment, isolation of power required and by whom, etc.
- Emergency arrangements, for example, requirements for firefighting and rescue, details of rescue equipment, etc.
- Monitoring equipment, for example, air monitoring.
- Details of PPE required for the work.
- A signature from the issuing authority, such as a/the manager, to confirm that isolations have been made and precautions taken.
- A signature from the supervisor of the work, to confirm understanding of the work to be done, hazards involved and precautions required, and that the permit information has been explained to all permit users.
- Extension and shift handover. The signatures of the authorising authority, manager, and supervisor for the permit to confirm the necessary checks have been made to ensure that the plant remains safe to be worked on and that all precautions remain in place. The new supervisors’ signature is also needed to confirm acceptance and confirm that the permit information has been explained to all permit users.
- Hand-back. A signature from the supervisor of the work certifying the work has been completed and the area has been made safe, including any required tests.
- A signature from the manager to confirm that the permit has been cancelled, all work under the permit has been completed and the area is safe.
Emergency Arrangements
After avoiding the risks associated with hot work and implementing safe systems of work, it’s important to set up and maintain any necessary emergency arrangements. Emergency arrangements must be well planned and set out by a competent person, and must be appropriate to the hazards generated by the specific work activities and environment.
Emergency arrangements must make up part of the risk assessment process and safe systems of work – no work should be commenced until the appropriate emergency arrangements are enforced. The complexity of the emergency arrangements will depend on the specific hazards identified.
Essential components to consider when deciding on emergency arrangements include:
- Raising the alarm. Employees must understand how to raise an alarm and communicate effectively during an emergency rescue. An effective, reliable method of communication that is regularly tested before work is commenced must be in place.
- Where deemed necessary by the risk assessment, suitable rescue and resuscitation equipment must be provided and those required to use it must be competent and fully trained.
- Safeguarding any rescuers. All rescuers must be competent in their duties, they must understand their role, be contactable and readily available at all times when on rescue duty and must understand that they should never put themselves at risk to enact a rescue. All emergency rescuers must be provided with the information, instruction and training necessary to ensure they are competent in their duties.
- Hot work activities pose a very significant risk of fires and explosions which must be assessed and suitable precautions taken. It’s important to consider all the hazards in the work environment and posed by the work activities and ensure that firefighting methods do not pose any additional risks – such as displacing oxygen in confined spaces.
- Whether plant may need to be shut down in the event of an emergency. For example, because the plant is the cause of an emergency or it is not possible to carry out an emergency rescue without plant shut down.
- Suitable first aid arrangements are in place.
- Arrangements for contacting and working with the emergency services in the event of an emergency. Employers must not rely on emergency services alone when setting out emergency arrangements. However, it’s important to consider how the emergency services would be informed in the event of an emergency, who is responsible for contacting them, and what information they might need on their arrival to ensure they can carry out their duties safely.
As described in this article, hot work can present significant risks. Employers have a legal duty to ensure these risks are assessed, controlled and monitored to keep their employees safe from harm. Where necessary and used properly, a permit-to-work is an extension of the safe system of work and risk assessment carried out for your work activities. It must never be considered a substitution for a safe system of work or a risk assessment, and must be followed by everyone involved.
What to Read Next:
- Hot Work Training Course
- Permit to Work Training Course
- Permit to Work Quiz
- 15 Workshop Hazards and How to Avoid Them
- What Is Arc-Eye? A Guide To The Dangers Of Arc Welding
- Welding Hazards in the Workplace: Safety Tips & Precautions
- How to Avoid Electrical Hazards at Work
- What Are the Key Differences Between Flammable and Combustible Materials?
- Welding Safety Quiz
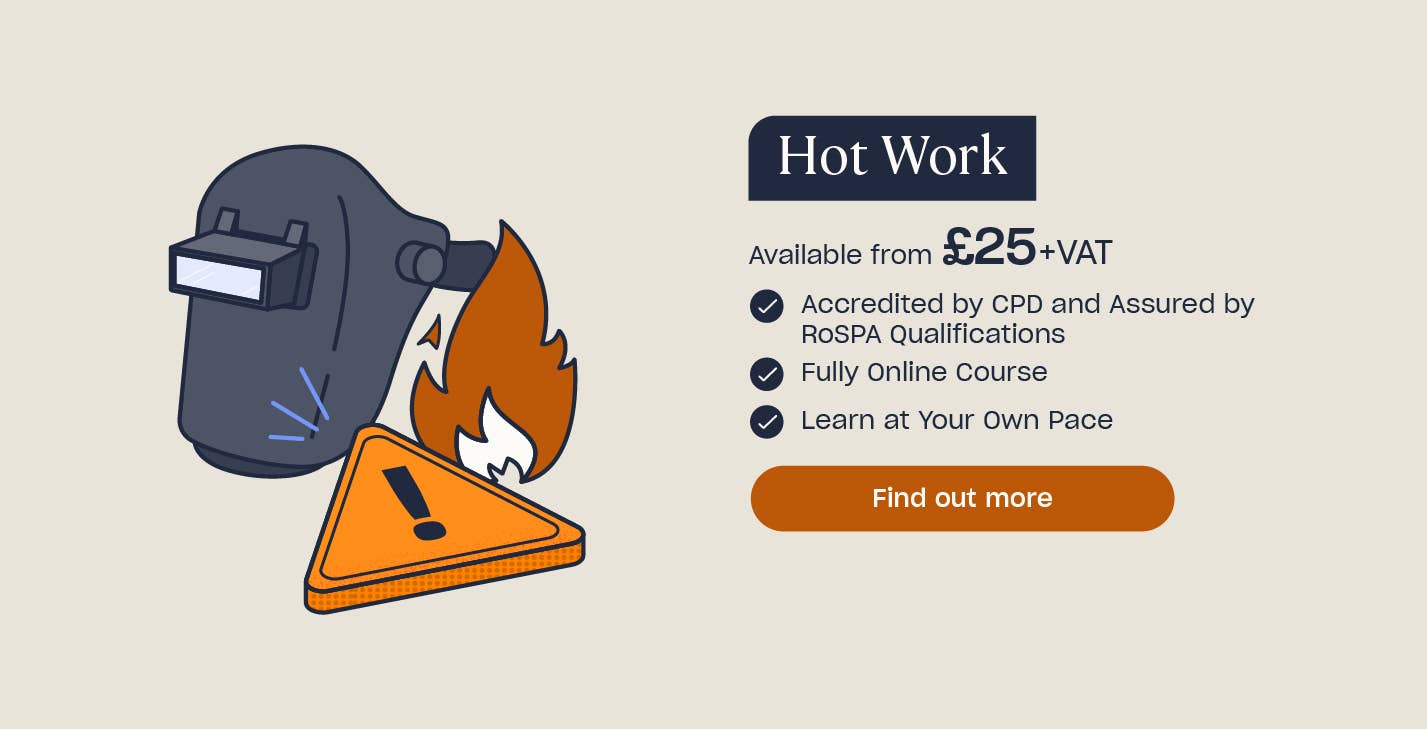
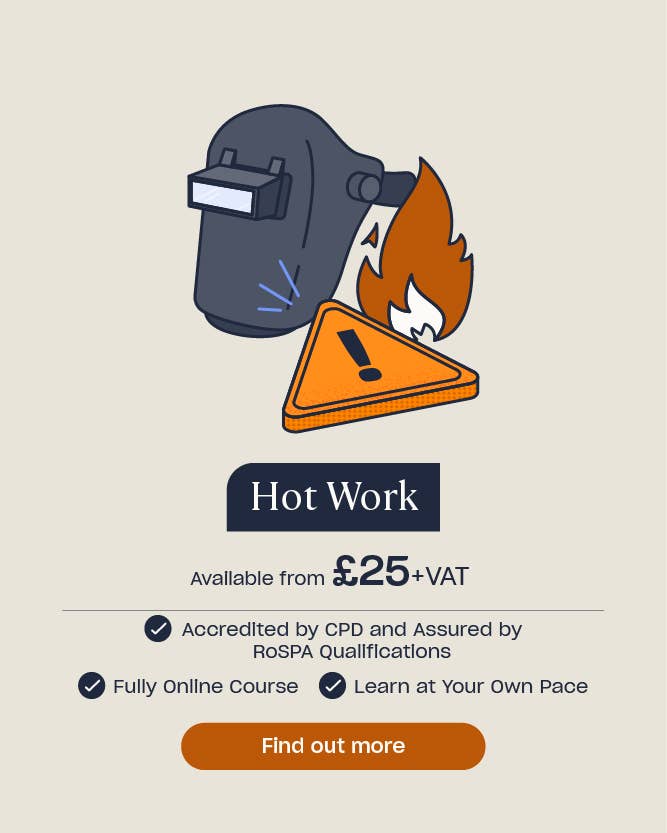